Why LSR (Liquid Silicon Rubber)
Normally thickness of diaphragm is a constant. But in LSR technology, thickness and pattern of each section can be defined by designer.
The flexible LSR injection unit is different from the various process designs. It can quickly sample and provide customer samples.
Overcoming the problem of adhesion between dissimilar materials through different structural design (biting) and process technology (surface treatment / self-adhesive)
LSR can produce optical lens with high temperature resistance properties (can resist heat < 180 degree C)
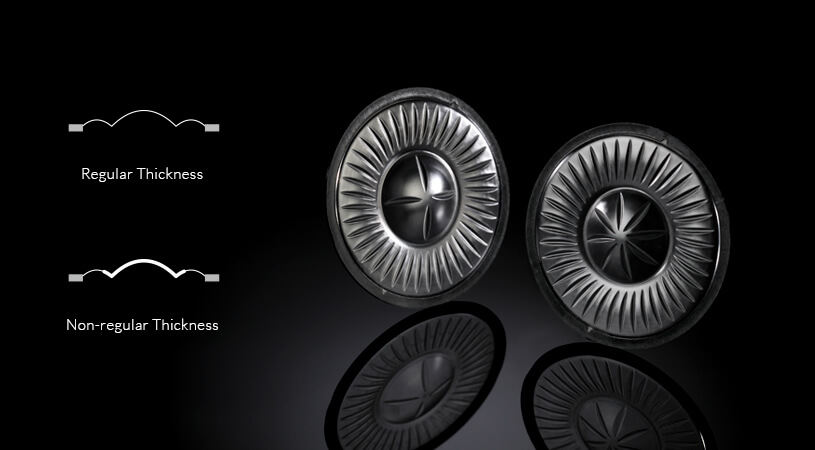
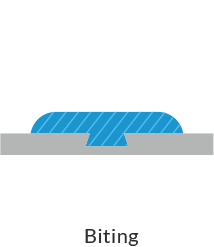

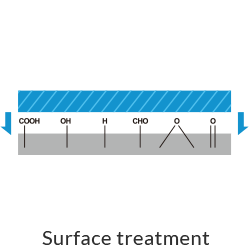
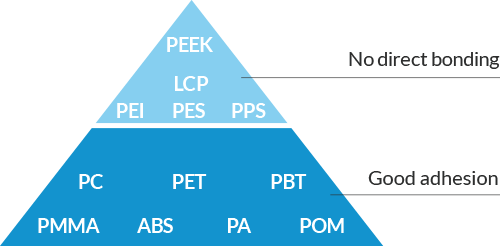
Advantanges of LSR
Excellent Heat Resistance: can withstand more than 10,000 hours of continued service at 200°C (392F).
Cold Resistance: can be used at –50 °C cold temperature.
High tear and tensile strength
Great flexibility
Weather ability
Exceed similar materials in insulating ability
Non-conductive
Radiation Resistance
Steam Resistance
Chemical, Oil and Solvent Resistance
Against Bending Fatigue
Vibration Absorption
Transparency and Coloration
Non-Stickiness and Corrosion Resistance
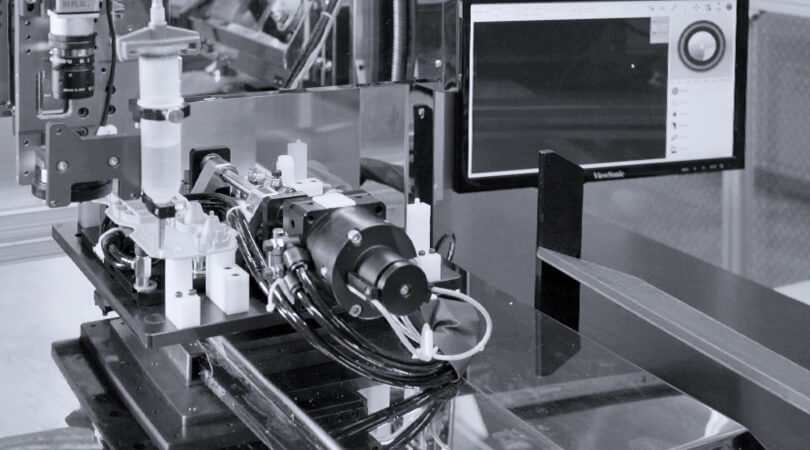
Core Capability
By well controlling the injection molding process with precision tools and all the high-end equipments, we can realize the designated contour to show the best image performance.
LSR technology for integrated molding
Molding Tool Processing: Precision Finishing< 0.002mm
Automatic: Design for automated production, yield > 96%
Quality Control & Record: Fully electronic monitoring and control system
Product Applications
LSR parts are not only for water proof and shockproof function, they can also be utilized as key structure for acoustic performance.
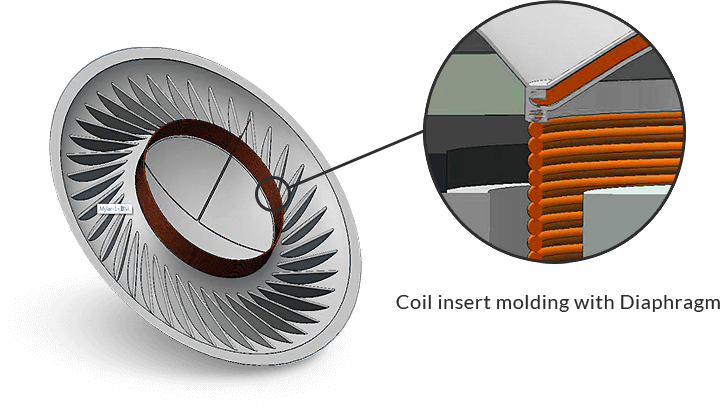
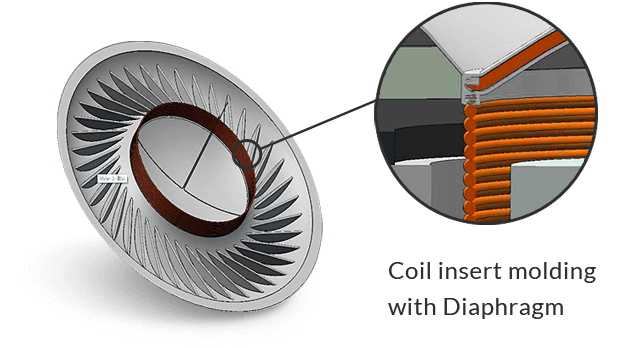